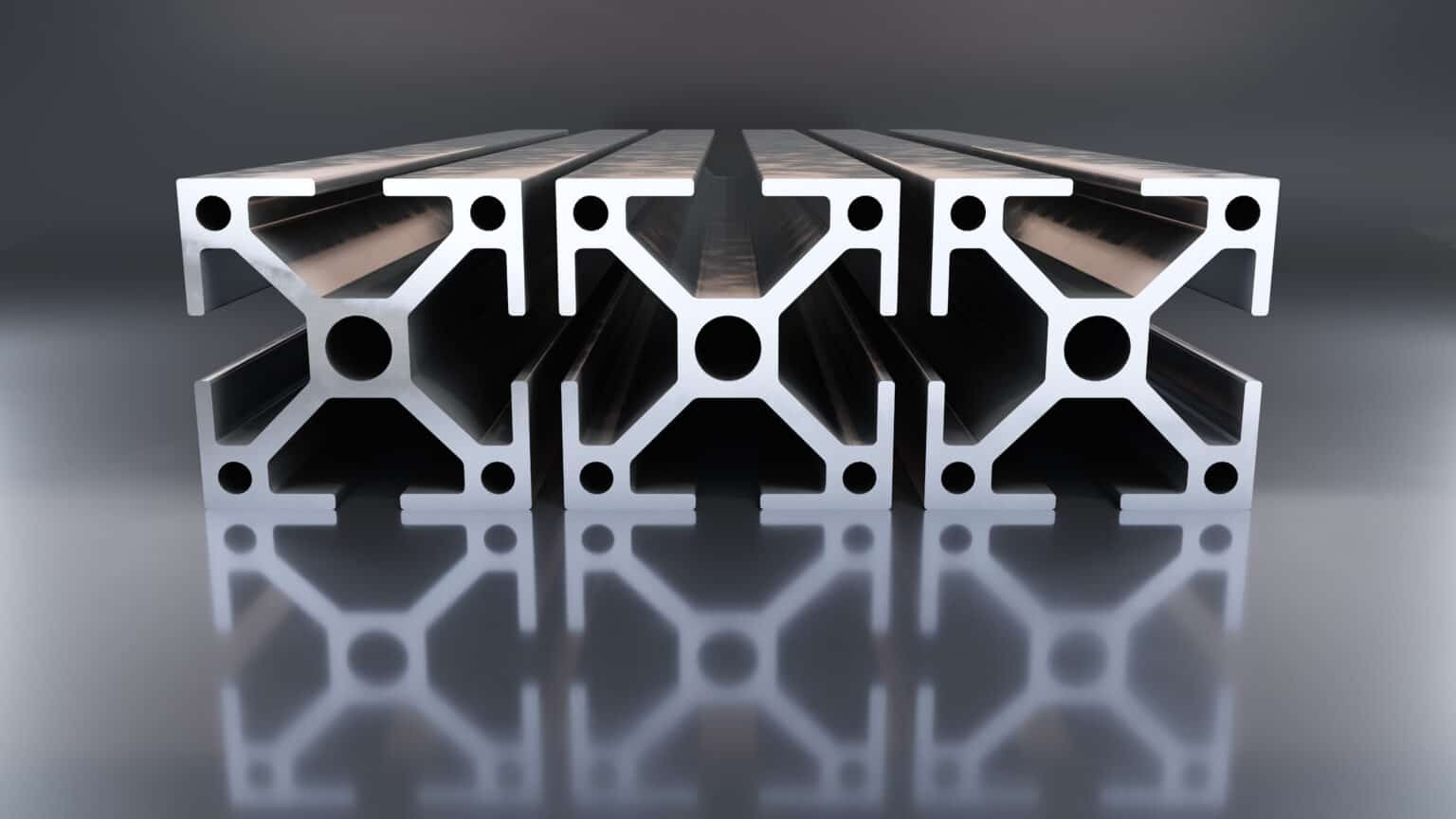
After the extrusion process is finished the aluminum profiles and parts are cooled down straightened to correct any deformities and then cut to the length. Additional treatments like anodizing or painting might be applied to enhance both the properties and appearance of the material.
Benefits of Using Aluminum Profiles and Components
Aluminum profiles and components come with a range of advantages that make them indispensable in engineering and manufacturing. Primarily aluminum is lightweight yet sturdy offering a strength to weight ratio that proves valuable in scenarios where weight reduction is critical such as in the automotive and aerospace sectors. This quality also contributes to increased fuel efficiency and reduced emissions in vehicles.
Moreover aluminum exhibits resistance to corrosion, which is crucial for components exposed to harsh conditions or utilized outdoors. The natural oxide layer that develops on aluminum surfaces acts as a shield against rust and corrosion extending the lifespan of the products. Additionally aluminum possesses electrical conductivity and heat transfer capabilities making it suitable for electrical parts and heat exchangers.
The adaptability of aluminum extrusion enables manufacturers to craft profiles tailored to specific requirements. This versatility allows for designing components, with shapes that enhance performance while minimizing material wastage.
Moreover aluminum is completely recyclable contributing to sustainability initiatives and lessening the impact of manufacturing processes.
Aluminum Extrusion Applications
The use of aluminum profiles and components spans across industries and sectors. In construction aluminum extrusions are employed for framing, windows, doors and structural supports due to their strength, durability and visual appeal. Additionally, the quality of aluminum simplifies the transportation and installation of construction elements.
Within the sector aluminum extrusions play a crucial role in producing components like roof rails, engine blocks and chassis where weight reduction without sacrificing strength is essential. The aerospace industry benefits similarly from the characteristics of aluminum by utilizing extruded parts in aircraft structures to enhance overall weight reduction and fuel efficiency.
Electronics manufacturers well as producers of consumer goods also make use of aluminum extrusion for items such as heat sinks, enclosures and display frames. The capability to create shapes ensures optimal thermal regulation and safeguarding electronic components. In the energy field aluminum profiles find application in solar panel frames and mounting systems where durability and resistance to corrosion are fundamental for sustained performance.
Advancements and Upcoming Trends
The realm of aluminum extrusion is constantly progressing due, to advancements and evolving industry demands.
One notable trend is the advancement of high strength aluminum alloys that deliver performance for challenging applications. These innovative alloys can endure stress levels and are especially valuable in aerospace and automotive sectors.
Another area seeing progress is the enhancement of extrusion methods through automation and digitalization. Today modern extrusion facilities are increasingly embracing automated systems to improve accuracy reduce production times and minimize errors. By incorporating technologies like computer aided design (CAD) and simulation software there is a greater focus on precise design and testing of aluminum profiles prior to manufacturing ensuring optimal performance while reducing the reliance on costly prototypes.
Sustainability remains a priority with ongoing initiatives to enhance the recyclability of aluminum products and decrease the carbon footprint associated with extrusion processes. Companies are investing in energy equipment and exploring innovative approaches to recycle aluminum scrap more efficiently contributing towards a greener manufacturing environment.
In conclusion
From factory settings to the structures of buildings and high performance vehicles the practice of aluminum extrusion plays a vital role, in shaping our modern world. The ability to produce long lasting and eco friendly aluminum profiles and components through this method highlights its significance across various industries.
With the progress of technology and the increasing need for creative solutions the aluminum extrusion sector is poised to adapt and grow tackling fresh obstacles with creativity and accuracy. Delving into the complexities of this procedure not showcases its current uses but also paves the way for upcoming advancements that will amplify its influence, on engineering and manufacturing.